Article and pictures by Phillip “Doc” Figdore.
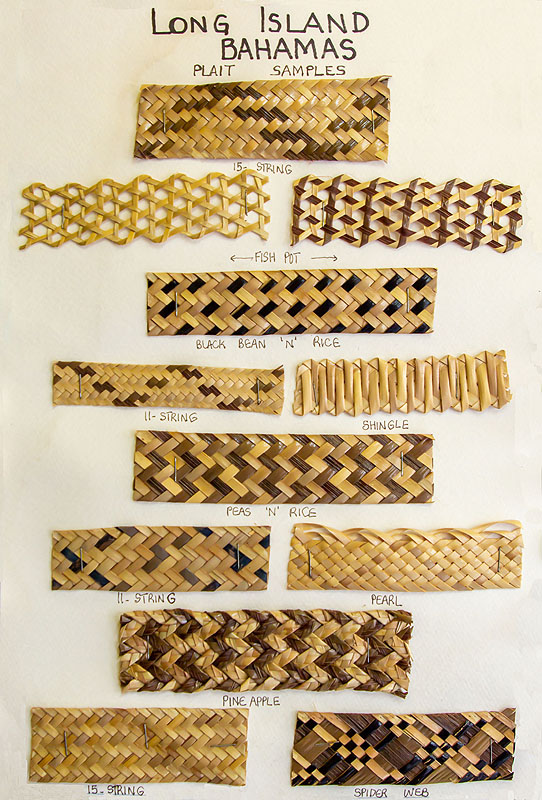
PLAIT. Dictionaries define it as “a single length of hair, straw, rope or other material made up of three or more interfaced strands” (Oxford Languages) with a typical example being “Joanne parted her hair, and then began to plait it into two thick braids” (Collins Dictionary).
Well, yes, and it’s not uncommon to see women, mostly younger, in The Bahamas with plaited hair.
But I wasn’t interested in plaited hair the Monday that I went to the Long Island Museum in Buckley’s. I was interested in that other plait in The Bahamas and for which Long Islanders are well known – straw plait.
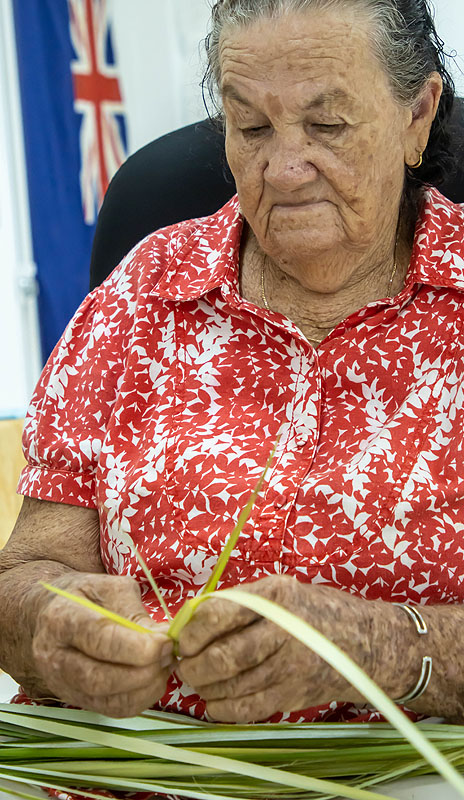
Organized by Patsy Cartwright, Museum Supervisor, and Sheena Cartwright, Museum Attendant, the Museum was hosting a week-long series (6/19-6/23) demonstrating the craft and art of plaiting with each day featuring different island artisans.
I wanted not only to learn about plaiting, and maybe even learn how to do it, but to hear stories.
So my first all-important question to Patsy, Sheena, and Isabella Knowles, Monday’s guest artisan, was “How do you say plait? Is it ‘plat (like flat) or ‘plate’ (like a dish)?” The question elicited chuckles from all three. Isabelle answered, “It’s ‘plat’, but seems most foreigners say ‘plate’.” So now I know.
The week’s other artisans included Eleanor and Pearl Cartwright (Tuesday), Patricia Darville (Wednesday), Oramae Pinder (Thursday), and Marjorie Cartwright (Friday).
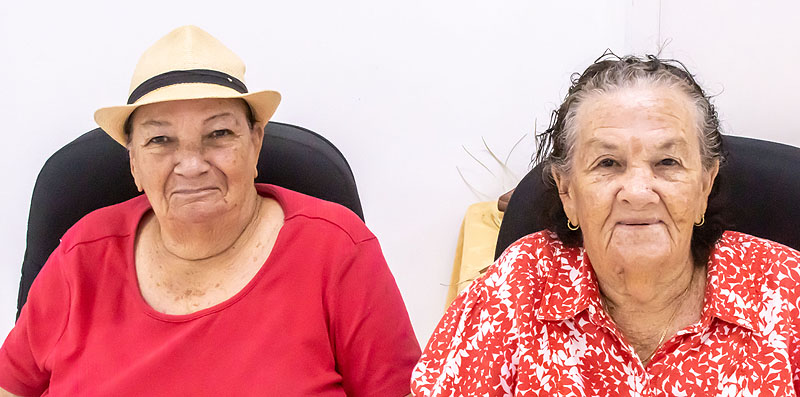
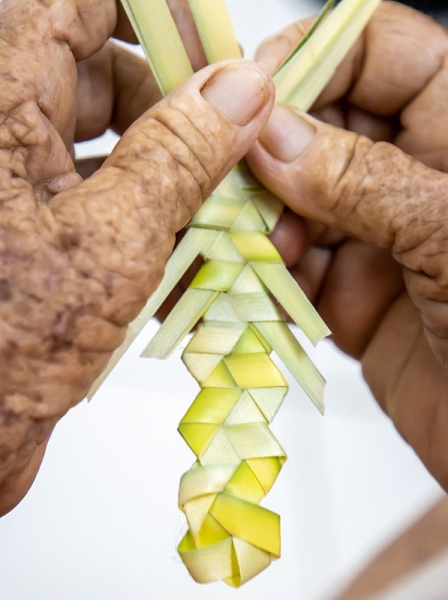
Each woman’s story, including Patsy’s and Sheena’s, was remarkably, and perhaps not unsurprisingly, very similar. They learned to plait at a young age, somewhere between five and seven, from a family member, usually ‘mommy’.
Isabella recalled that her brother would carry her on his shoulders, visiting family and friends, and while watching them plait, she just “picked it up.”
For all of them, plaiting was not just a pastime but rather, a necessity to bring in extra income, albeit small.
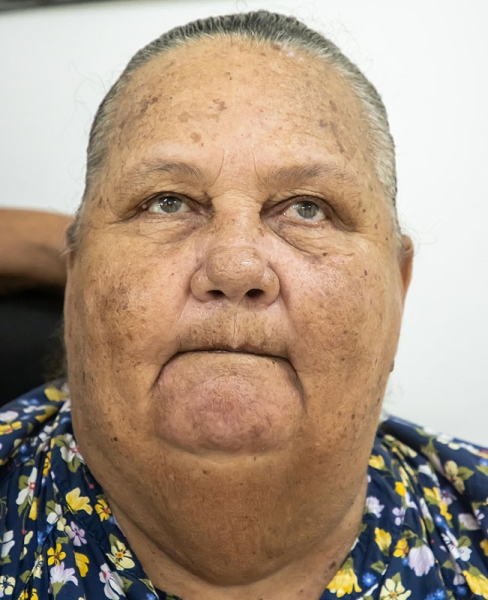
When these women were children it was a means to get needed pocket change for school supplies. Considering that as a group, they would have been in school in the 1940s, ’50s, ’60s, and into the early ’90s, it speaks to the self-reliance of islanders, and the centrality of the family, with every family member contributing.
Their teachers, i.e., mothers, were all perfectionists. Oramae related that her mother always said “Set your plait”, meaning pull the strands down against each other so that they were nice and tight, and that she didn’t accept less than the best.
No holes were allowed in patterns that weren’t supposed to have holes. Patricia said that her mom would “cut her butt” and tear the plait apart if it didn’t meet her mother’s standards. This standard of perfection may be why today’s plait from Long Island is so sought after.
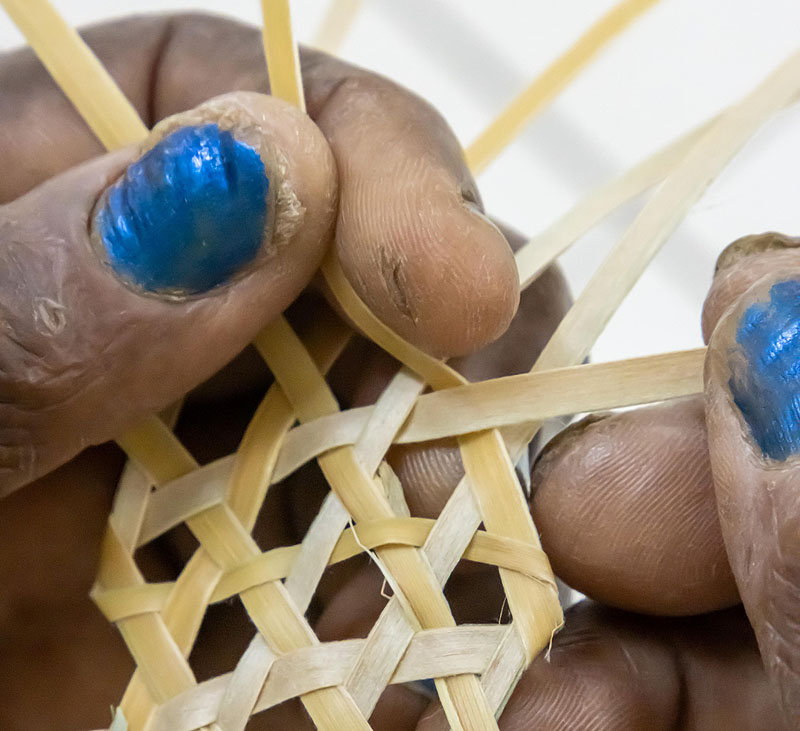
The women all have go-to standards of maybe ten or so patterns. Eleanor and Pearl said that there is probably no pattern that they can’t do, given some time to think about it.
However, they find ‘fish pot’ the most difficult and just won’t do it, whereas it’s one that Patricia can do almost blindfolded.
As for smoking straw, only Oramae and Patricia will do it.
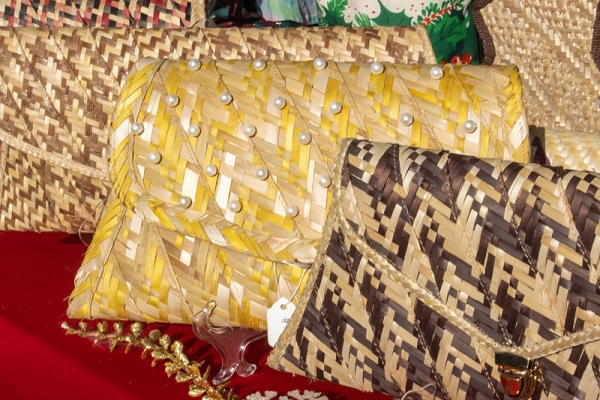
FROM BUSH to PLAIT
The beautiful handbags, straw hats, placemats or other straw works that you might see at local roadside stands, local island straw markets, or the BIG ONE in Nassau, are the end product of many hours of hard work, careful attention to detail, and creativity.
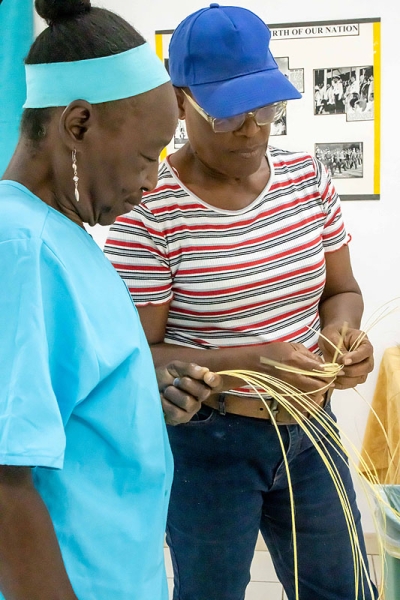
All these artisans are independent businesswomen playing an indispensable role in the ‘supply chain’ of getting palm leaves from the bush to the final assembled product.
Now Oramae is the exception in this group, as she is a member of a collective of crafts women called Starfish Traders based in Seymours. So most of her work is used by the group rather than being sent to off-island clients.
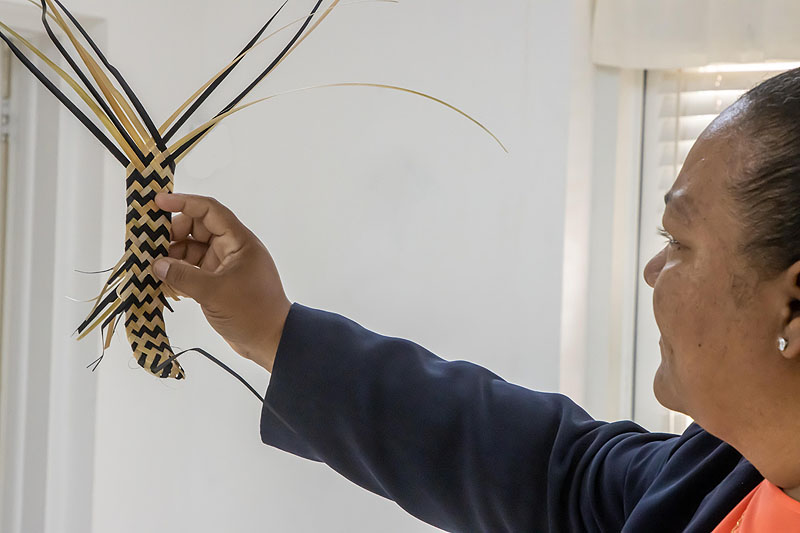
So where does it begin?
In the bush. The silver top palm is the favored palm of these Long Islanders. The name derives from the silver appearance of the underside of the frond. A trip into the bush is required to find the best palm fronds. Only certain secret locales produce fronds of the best quality for plaiting.
The more mature women relegate this task to younger folks as trekking through the thick bush and then cutting out the fronds is laborious. Timing is critical as the fronds can’t be cut if too young or too old.
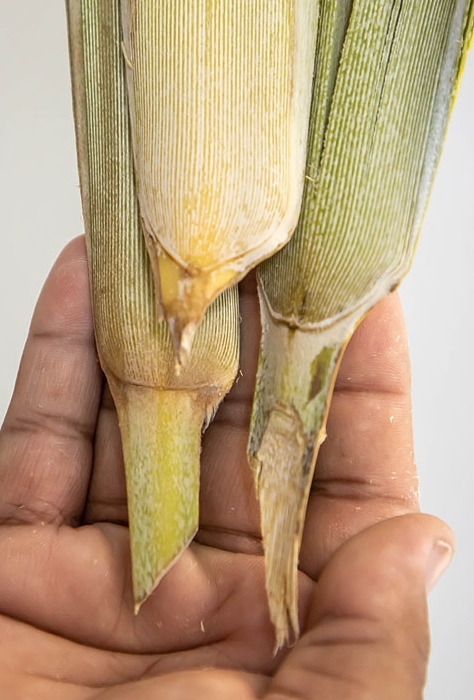
Careful cutting or clipping is required to keep the palm healthy. Sheena commented that in her treks through the bush, she’s seen the tops of palms that have been “whacked to death” by harvesters who didn’t know what they were doing.
Sheena provided the following link to an excellent video produced by The GUANIMA Project, not only on what the palms look like in the field, but how they should be harvested to maintain a healthy and sustainable crop:
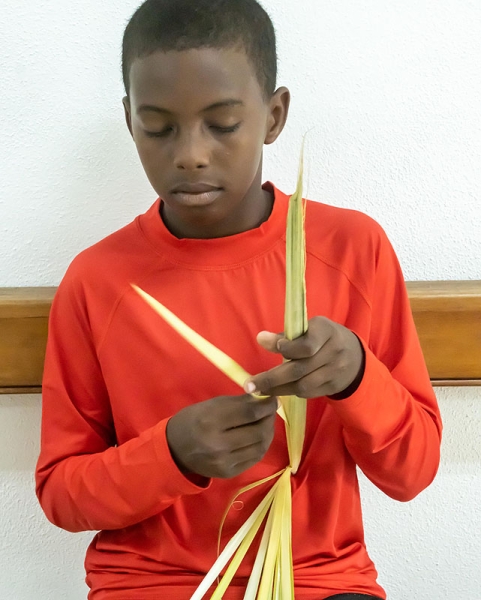
The fronds are taken home and put out to dry. Depending on the number and space available, they may be hung up like clothing or put out on rocks. The fronds get separated into single ‘leaves’ (properly called blades) which are then opened and split into two.
Although not difficult to do, when split, the blades produce very fine dust which can cause itchy eyes, coughing, and runny noses for those with allergies and more severe reactions for those with asthma.
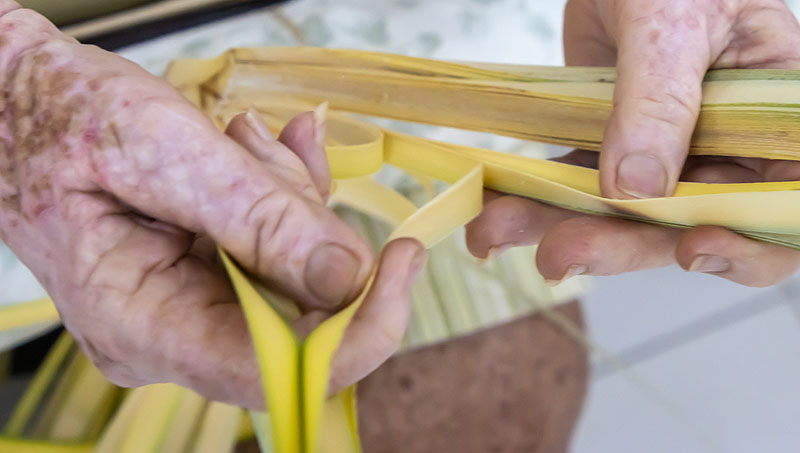
The blades now get slit, that is, cut into small strips. Using a very fine and sharp knife, the rough outside edges of the blades are removed, and then strips are made of the desired width.
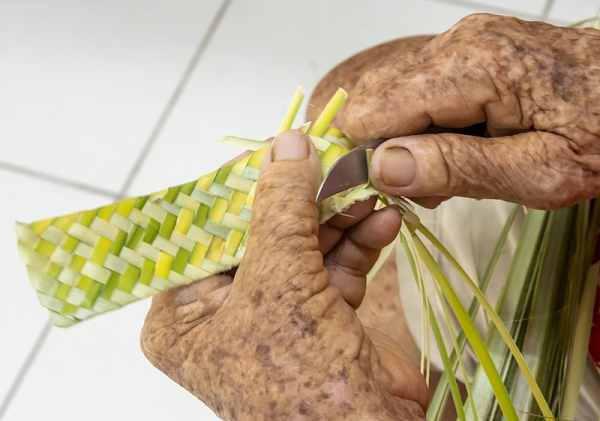
Consistency here is important. No matter what width is needed, from narrow to not so narrow, each strip must be the same width to give a tight and neat plait.
And for these women, rulers aren’t used. It’s all done by eyeball with years of experience backing them up.
At this point, the artisan has several choices: use the straw as is, peel and use, dye, peel and dye, or smoke it! So many choices. It’s important to know that there is a right and wrong side to straw. If you closely examine the straw you’ll see or feel that one side is ‘smooth’ and the other ‘rough’. For very fine and more exquisite plaits, the straw is peeled separating the rough from the smooth side giving a very thin smooth, soft piece of straw.
Dyeing is done after stripping or peeling. A large pot of water with no additives is brought to a near boil, dye added and mixed to make sure it dissolves – then straw is added and the water kept at near boil for, well… each artisan had their own number of minutes. The pot is then allowed to cool. And like dyeing fabric, the straw is kept in overnight, removed, rinsed with water to remove excess dye, then allowed to dry, but this time not in direct sun to prevent fading.
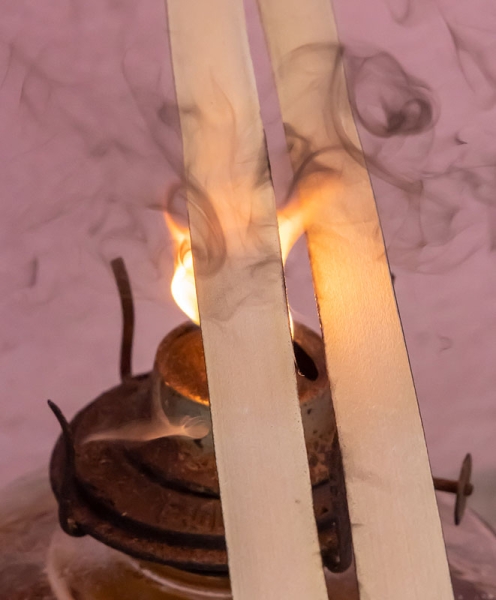
Smoking straw is its own tedious, messy, smelly, and of course, smoky process best done outdoors. The straw’s smooth side is passed carefully across a kerosene lamp’s flame. Care must be taken so that the straw is only charred but not burnt while also allowing the lamp’s soot to deposit on the straw.
A rough guide is to hold the straw just close enough to the flame that it is just visible through the straw. Too close will result in setting the straw on fire, and too far away and the straw won’t get charred.
Smoking can only be done one straw at a time. After charring, the straw must be wiped with a cloth to remove the soot. The result is an absolutely black and shiny piece of straw. And it must be used immediately since smoking the straw drives out moisture and the straw can get too brittle if left unused for too long.
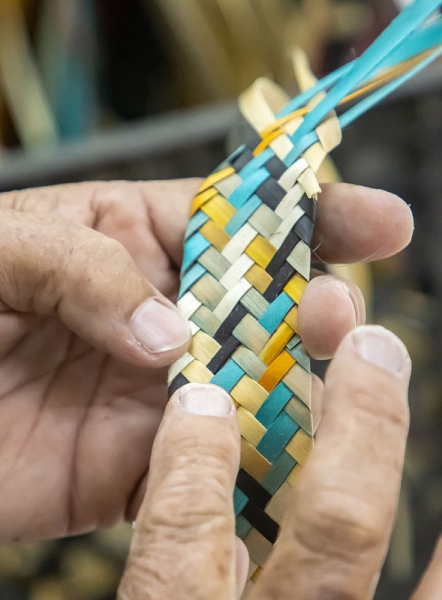
Now, finally, actual plaiting can begin. There may be 100 or more patterns, and although the underlying straw pattern (weave) such as a simple 11-string or 15-string may be the same, the addition of dyed or smoked straw changes its appearance and may even change its name.
These women have clients who will typically place orders and specify pattern, width, color, yardage, etc. Although in this 50th anniversary year, many created one-off designs for their clients’ consideration.
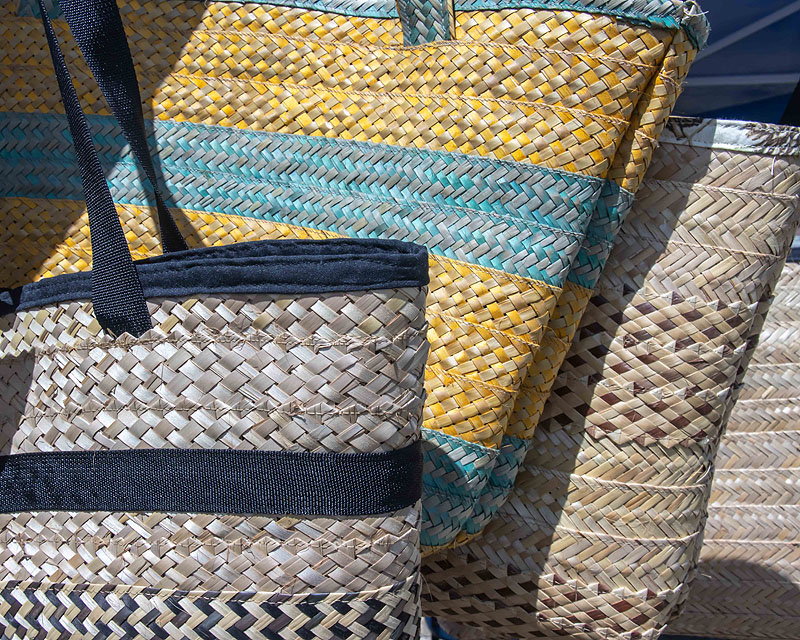
It takes about 20-25 minutes to plait a yard and clients will purchase about 20-30 yards at a time. An average-sized lady’s handbag might require 12 yards of plait, so before the plait is sewn together, there’s already four to six hours of creative talent put into the plait itself, without accounting for all the prep work.
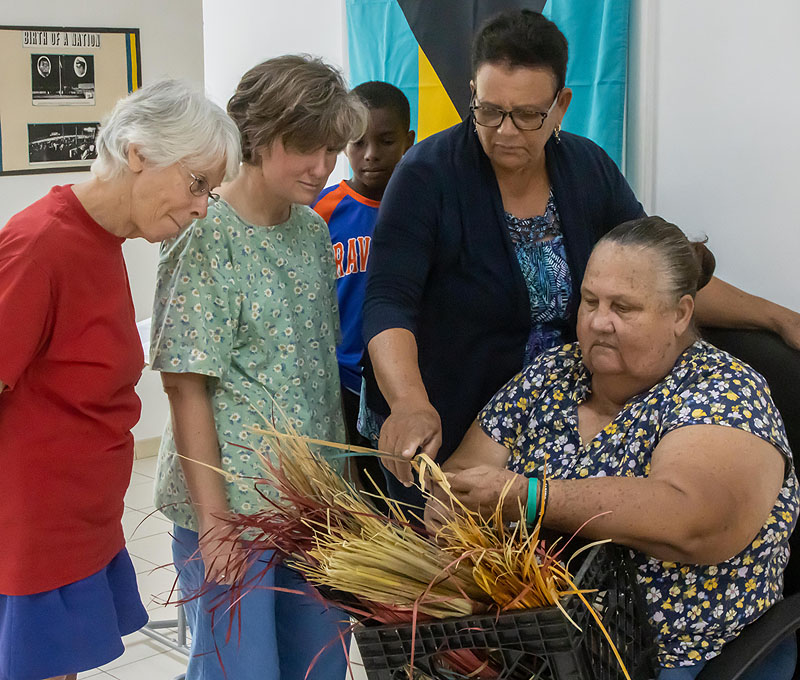
WILL PLAITING BECOME A LOST CRAFT?
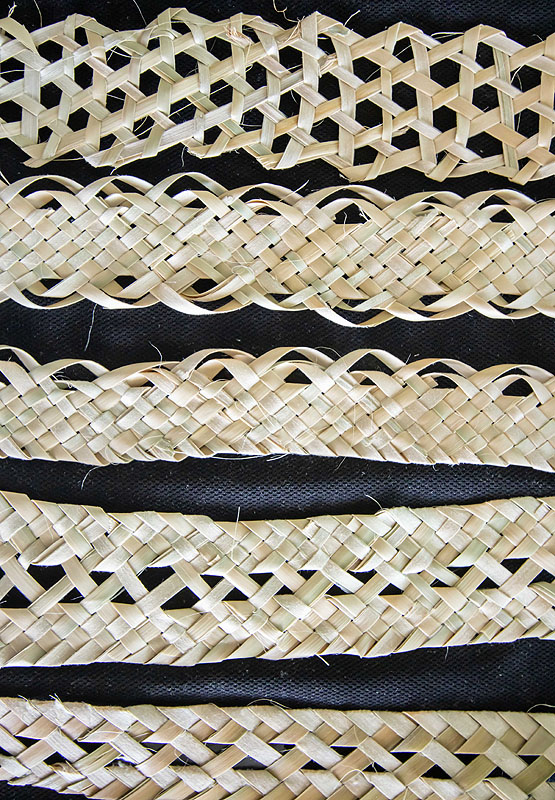
An easy question with no easy answer. From what these women have said and from what I’ve seen on the island, it could very easily be gone in a generation. Every single artisan as well as the Museum staff learned to plait. The Museum has a wonderful binder containing photos of Long Island plaiters and samples of their work. Sad to say, most are now dead.
It was instructive to watch Patsy and Sheena pick up straw and begin to plait. Like many skills, although you may not have done it for quite some time and are a bit rusty at the start, you quickly remember how to do it. Dishearteningly only Patricia said that three of her four children were picking up the skill. But three is better than none.
Malachi Johnson, a very young man of about ten from Hamilton’s, was there for the whole week and by Friday was looking rather proficient. Let’s hope he stays with it.
There are many reasons that this craft is not being transmitted to ‘youngsters’ – it’s not ‘exciting’ or ‘cool’ in this world of computers, internet, cell phones, computer games, cable TV, etc., and most importantly, as for so many artisans and craft people, there’s not much money in it.
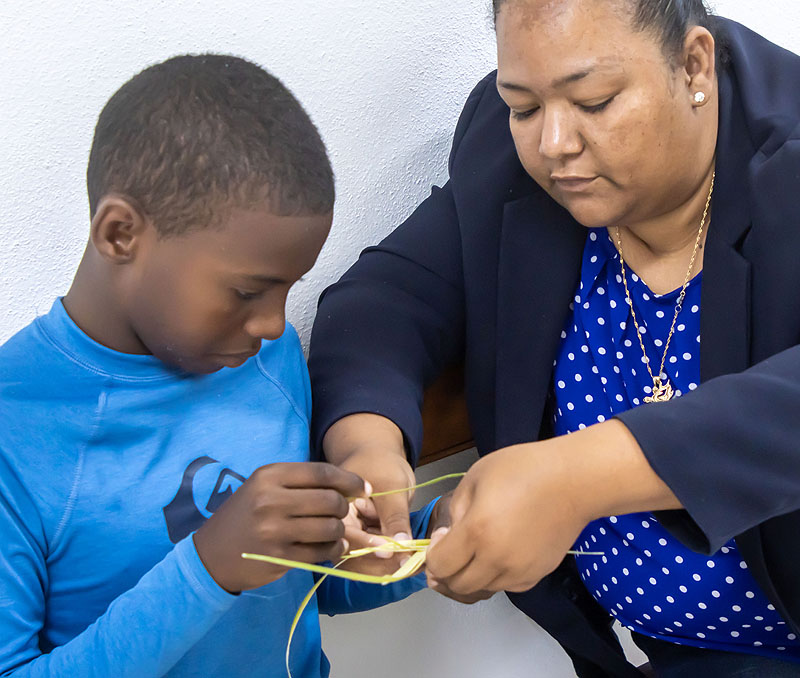
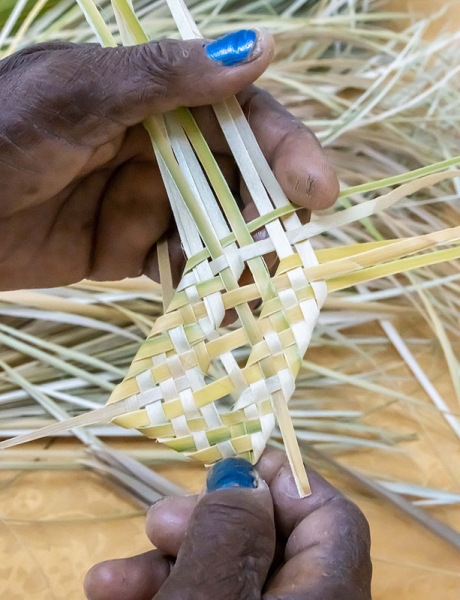
What can be done to ensure that Bahamian plaiting does not become a lost craft so that when you walk through LPIA anything made from straw says “Made in China?”
A national craft (plaiting) guild that approves and rates artisans? Local island craft collectives such as Starfish Traders on Long Island, but expanded that do the same? One or both? Establish a directory of all plaiters on each island, whether they sell finished items locally or send plait off-island for finishing?
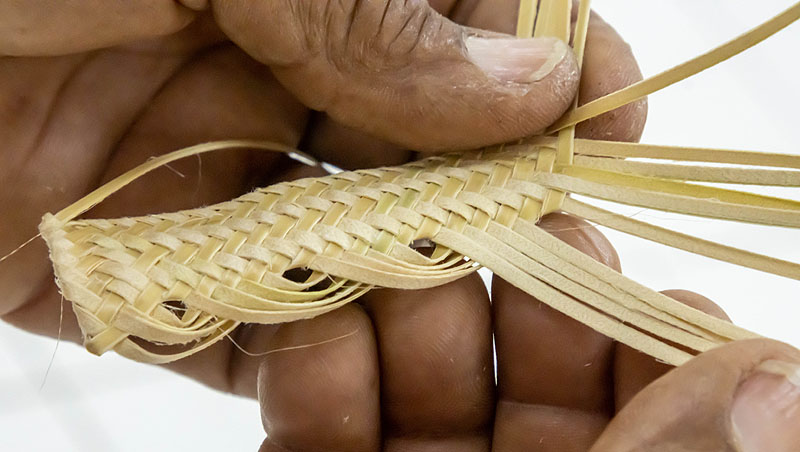
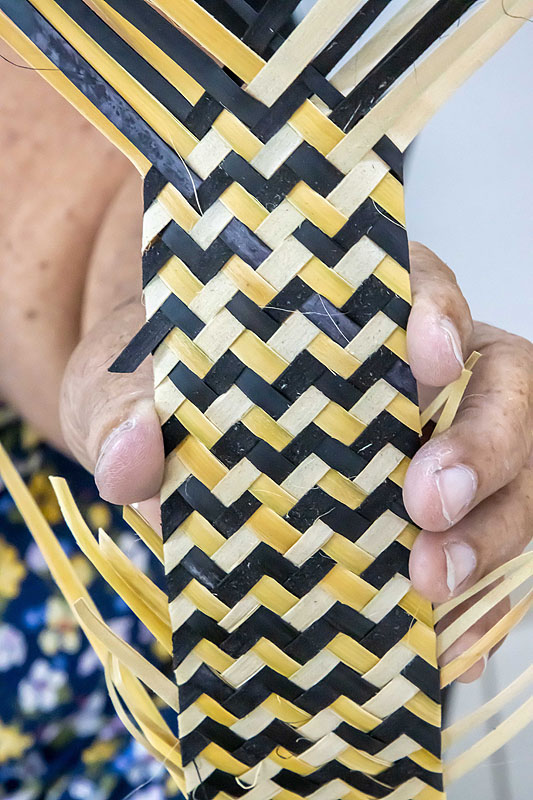
Setting prices so that the craft person receives fair compensation for their work? Personally, I’ve always felt that much of the out-island crafts were underpriced and when I hear someone trying to haggle for a lesser price, I want to take a baseball bat to their head and say “Do you know how much time and talent went into that? Would you make that for that amount of money?”
For Long Island, a central straw/craft market, similar to the downtown market in Georgetown, Exuma would be a great addition. But where on Long Island? For Exuma, the choice of putting the straw market at the “square” was a no-brainer, what with all the road and foot traffic that goes past. Long Island has no real central shopping area.
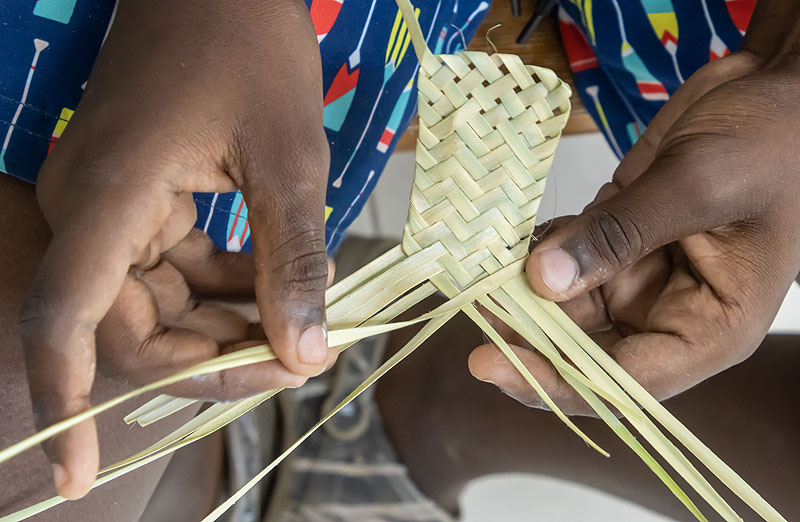
Putting a market just outside Deadmans Cay airport makes some sense. The Calypso Cove cruise port going in at Gordon’s at the extreme south and talk of relocating the airport to the south puts a damper on that.
Creating an internet portal for direct sales to other countries (yes, shipping could be an issue)? Teaching it in primary and secondary schools? Perhaps the University of The Bahamas (UB) Department of Visual and Fine Arts could offer courses in the art and craft of plaiting.
The book “Bahamian Straw Craft – A Guide to Making Native Straw Bags” is considered to be “the Bible” for this craft. Authored by Isabella’s niece Barbara Knowles Jesubatham, the book was written for the express purpose of “…preserving this Bahamian cultural tradition, by educating present and future generations.” How about putting this book in every school and library across The Bahamas?
Sailing was just named The Bahamas’ national sport in recognition of how sailing and boat building have been central to The Bahamas in years past and to the importance of preserving that tradition. Perhaps it’s time to name plaiting as the national craft of The Bahamas to help preserve it.
Thank you so much! This was an excellent article which l will also share on our Creative Nassau Facebook page! The harvesting video that you referenced was produced by GUANIMA PRESS for CREATIVE NASSAU as a part of our work for the PlNE ISLANDS PROJECT. You can find the free links to that video as well as another 12-minute history of straw documentary written by Patricia Glinton Meicholas, VP of Creative Nassau, and much more on straw at our website http://www.creativenassau.com. Bahamian straw craft was one the our main focal areas which allowed us to obtain membership for the City of Nassau in the UNESCO Creative Cities Network in 2014! We also teach straw plaiting and weaving classes at BTVI in Nassau….stay tuned for the next class dates!
Thanks for the link. Will add it to my list.
I love it
I love it
Author of Bahamian Straw Craft
Where can I purchase the stripe of plaits.
Those are available at Long Island Traders located in the Bight, Long Island. They have a Facebook page.